Sharing all to progress
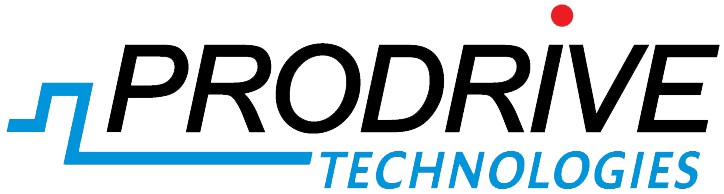
You have probably read a lot of stories in which it is insisted that workplace innovation is about respecting the tacit knowledge of the employee and that companies need sophisticated engagement policies to let these employees bring their talent, knowledge and effort to the company. Nothing could be more wrong! That is if you want to be real world competitor. You need create to an environment in which all of your employees share their tacit knowledge with their colleagues and with the company. It is by sharing everything you know and have that will give a company the real lead in the market. Companies that can achieve this state discover that there is huge potential in building on sharing economy principles.
The Dutch electronics company Prodrive Technologies has achieved such a level of sharing. The company is a marvel in the Eindhoven area in The Netherlands. It is surrounded by Brainport, the Dutch High Tech Campus, the StartupBootcamp and other sharing experiences in the ‘smartest region of the world’. But the real advantage the company has achieved lies in its capacity to create a building knowledge experience.
Prodrive Technologies has consistently been one of the fastest growing companies in its sector, with more than 10% growth in turnover each year since its creation in 1993. Some 600 engineers are manufacturing electronic equipment aimed, for example, at high end computing, industrial automation, motion and mechatronics. Part of the growth is by reshoring manufacturing production from other parts of the world.
You can bet that many competitors would like to know what their secret is. And the main thing is that this company does it all by rowing against the tide of management philosophies.
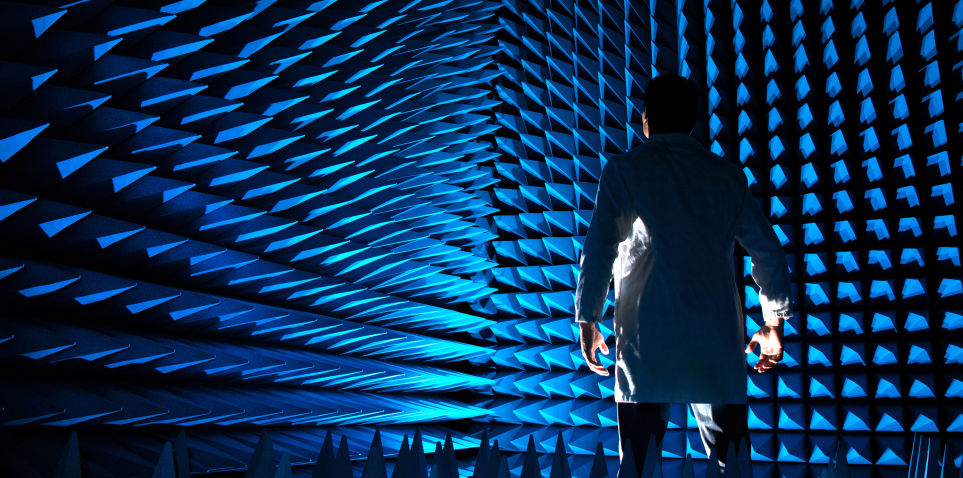
A first principle is that the company does everything in-house: from design to manufacturing, from cleaning to catering. If you want world class products, then you are not going to treat your employees in the cheapest fashion possible. Production is 24/7, so you need a constant support for your employees and engineers. Total control of all aspects of production gives total control on quality, on speed of production and service reliability. No need to check supplier networks or to draft lengthy contracts.
A second principle is that you can only make progress if everyone understands that you, as a member of the company, need to share all your knowledge about products and processes. It doesn’t help to be protective about what you have learned. The company has installed procedures to help standardize all the learning by first-line engineers. All this learning is shared and improved by colleagues. In that way the speed of continuous improvement of the company is seriously strengthened. The company also insists on knowing everything about its production. The software for all acquired robots and other computer controlled machines has been rewritten by its engineers. The company does not like to rely on software engineering that it does not fully understand.
A third principle is that the company has abolished the distinction between service and production work. If you ever visit the company you will be amazed by what you will see. From the outside, the building just looks like any other office building. But on the inside you will find that each level of the building hides a whole bunch of highly automated production cells, all in a clean and low noise environment. Production is supported by robots, automated guided vehicles and automated control systems. And the operators are in fact all highly trained engineers. You can’t find a distinction between office and machine work. So, for engineers it is natural to be in the production environment. In such a set-up the distinction between blue and white collars is a thing of the past.
The company prides itself in working in a fundamentally different way to other companies. The three principles shows how the company differs from what still is the main message in management manuals. It is also uncommon for a company to put on its website that profit is not its main aim. Prodrive Technologie aims for sustainable progress. The website shows many other results the company has achieved over the years. The motor of the change is the way people work together and help each other invent the future. The formula for making progress is to start with an agreement to share. And the company is truthful to its own philosophy and has agreed to give you, as member of our growing workplace innovation community, a glimpse of what is happening in the company.
We hope you are inspired by their approach to workplace innovation.
Steven Dhondt – TNO, The Netherlands