Aveiro, Portugal
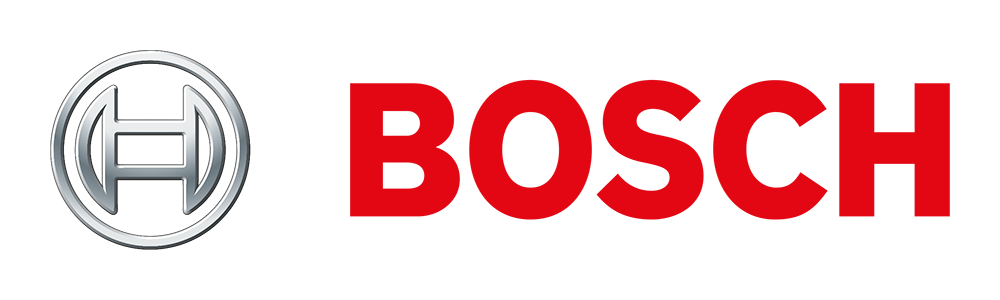
Bosch, the multi-national engineering company which operates in the automotive, appliances, power tools, security systems and solar energy sectors has been manufacturing in Portugal for over 100 years. Its five locations in Portugal have over 3000 employees out of a global headcount of more than 290,000. In 2014 it recorded sales of €788 million.
It is also one of the leading companies in Portugal in terms of employee involvement.
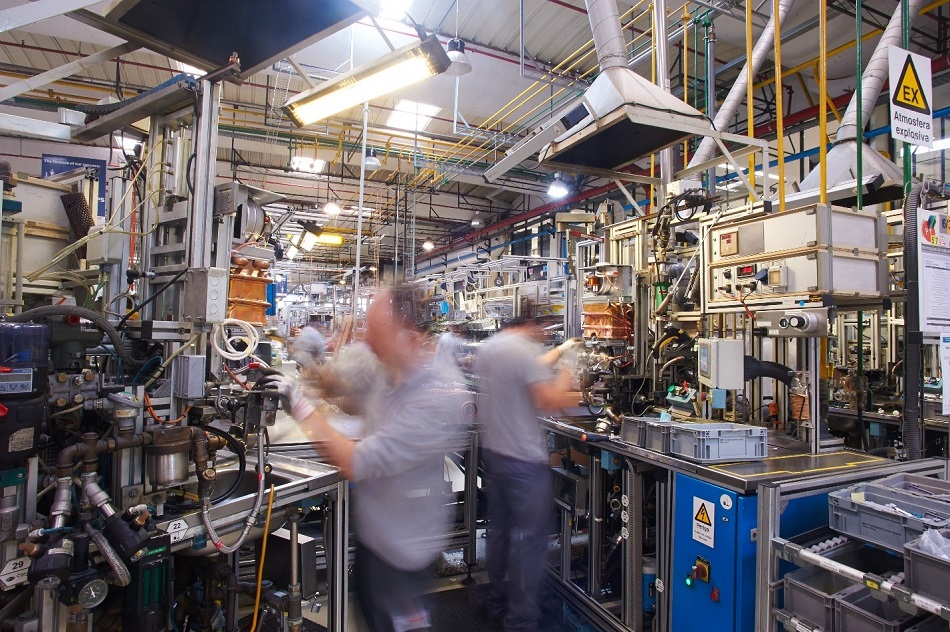
A people-centred approach to LEAN Management
Interviews conducted by UK WON with staff at all levels at Bosch Portugal from senior management to frontline workers (Associates) revealed remarkably consistent responses and a common commitment to open communications, team working, knowledge sharing, mutual support and continuous improvement.
This cohesion reflects the recognition that the business can “no longer go for universal solutions because customisation is more and more a focus” so small improvements in products and processes must be constantly made by everyone.
The company is committed to a programme of people-centred LEAN Management aimed at driving out waste and improving efficiency. Associates are closely involved in identifying issues and opportunities for employee-driven innovation. Problem-solving becomes a tool for empowerment and connecting with management.
Daily meetings, which are strictly time controlled, are designed to review Key Performance Indicators – what happened previously, what needs to be achieved and with what resources, what are the priorities and what will hinder performance and progress? White boards are used to visually represent the outcomes of the meetings and actions required as well as giving management a snapshot of on-going activity.
“We are not only saying that management now understands better what the team is doing, we are saying that the team knows better what the other ones (their colleagues) are doing.”
Anabela Rodrigues, Logistics Manager
These short meetings also act as a cohesive influence connecting management and front-line staff, creating mutual respect as together they strive for continuous improvement. Although senior management don’t attend every meeting, their regular presence reduces any notion of management remoteness and reinforces the value that Associates brings to the decision-making process.
“Every day we are close to people, close to where everything happens which is on the shop floor.”
António Conde, Industrial Director
Daily meetings are supplemented by a quarterly workshop which undertakes a more strategic review of business performance. These are increasingly being coordinated by Associates, and evidence suggests that this has had a profoundly motivating effect.
Training and coaching are equally valued as catalysts for innovation. Trainees are encouraged to query traditional ways of doing things and this produces new ideas and new efficiencies.
“When people sometimes are doing the same process for three or four years every day it starts to be difficult to identify where we have to improve.”
Anabela Rodrigues, Logistics Manager“The continuous training that we receive here is the thing I think is the most important part for me loving to work here.”
Francisco Cristo, Works Council Health & Safety Representative
Coaching is used to bring managers closer to Associates ensuring they are able to develop employee skill sets. It is also seen as a kind of empowerment that develops the Associate’s ability to perform a wider range of tasks, take on additional responsibility and add more value.
Bosch also has a successful suggestion scheme which is in the process of going paperless. It is founded on the principle that every suggestion is analysed for feasibility, both practical and financial, and each gets a response – even those that are eventually rejected. Positive suggestions are rewarded.
“Innovation for products and process are not just the work of a few persons, everybody should have the opportunity to give the ideas regarding improvements that we can make in the process or in the product. So we have a system in place where each one of our Associates is able to give ideas about quality, about products, about process, about safety.”
Paulo Vieira, BPS Coordinator
In one case, the company made substantial savings which they shared with their customer when someone recognised that the use of five screws on an appliance accessory could be reduced to three.
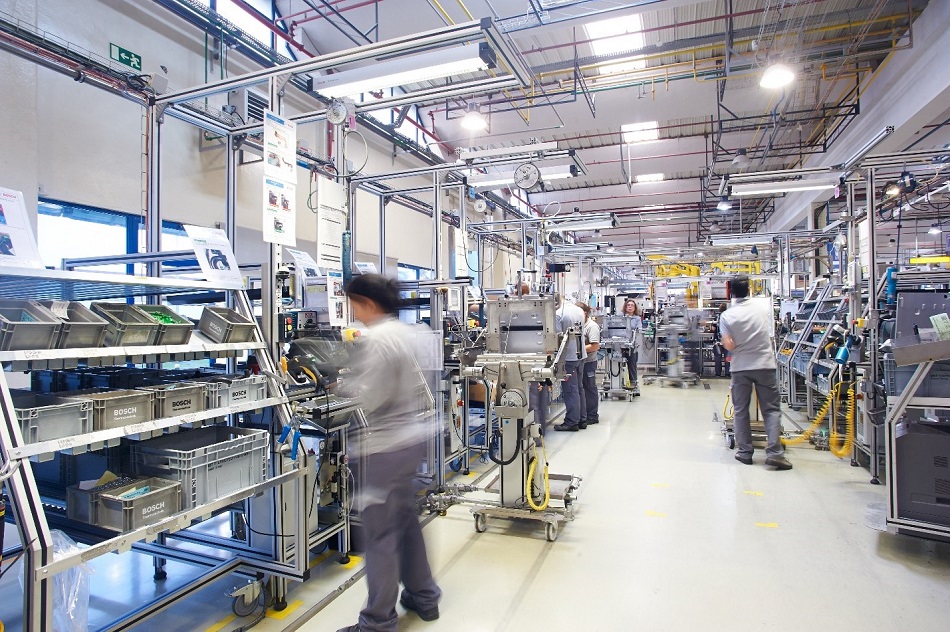
LEAN Management – changing mindsets and empowering staff
According to the LEAN Management Project Team’s Nelson Ferreira, LEAN Management is a new way of leading people which requires a significant change in culture and management mindsets. It impacts both on the individual and on the team as a set of people working together. This is achieved by the daily alignment meeting where people share their challenges and where they are able to offer support to their colleagues, even to share knowledge about processes where they are the experts.
Designing the programme revealed that Associate satisfaction and performance are related, enhancing team working and workload sharing.
Associates are involved in the development of the LEAN Management programme through workshops where they have a say in strategic planning; by being job-shadowed (which Bosch calls ‘Sit-ins’) to establish how processes perform and identify good/bad practice; and by leveraging the performance of the whole team by bringing best practices and ideas from one Associate to another and incorporating them in a common knowledge base.
Managers also become more connected with the challenges that their Associates are facing and this gives them more tools for future strategic decision-making and for improving team performance.
Empowerment at Bosch is clearly related to associate involvement. Production Director António Conde feels strongly that this is the key to positive change.
“Getting everyone into the process of solving some problem, finding a new solution, this is empowerment. Involving the people, hearing them, giving appreciation for their contribution, this is empowerment. It’s having everyone on board, everyone on this continuous improvement machine.
“LEAN is very much based on standards, rules. Normally we think that rules can hinder a little bit the creativity and innovation process. Honestly it’s the other way around. LEAN has always a purpose, it’s the customer. It tries to view or observe things from the customer perspective so it does not hinder the creativity. It just helps you to focus on what the customer will value out of that creativity focus. So actually with LEAN I believe we are more productive in terms of creativity, innovation and development of new processes, new products because it really helps you to focus on what really matters, the customer.
“If you apply it right LEAN is not about black belts or gurus or hot-shots that know all the toolset. LEAN is about the mindset, it’s about a culture, it’s about removing waste, it’s about continuous improvement. And this is achievable only when you have everyone on board from the shop floor associates to the top management.”