SOUTH KOREA
The Future of Workplace Innovation
In May 2023 the Korea Labor Institute (KLI) organised “The Future of Workplace Innovation” conference, the purpose of which was to strengthen the WPI-foothold among Korean businesses. The conference was opened by the director of the Labor Policy Office of the Korean Ministry of Employment and Labor, and participants included representatives from Korean business, government, policy making and science.
A point of departure for the conference was a comparative research study commissioned and carried out by KLI’s research fellow Dr Seri No, to which contributions were made by international researchers from Germany, Japan, Netherlands, Scotland and the USA. The researchers, among them Hajo Holst (for Germany), Peter Totterdill (for Scotland) and Peter Oeij (for Netherlands), presented their insights to the Korean audience, leading to lively discussions and debates.
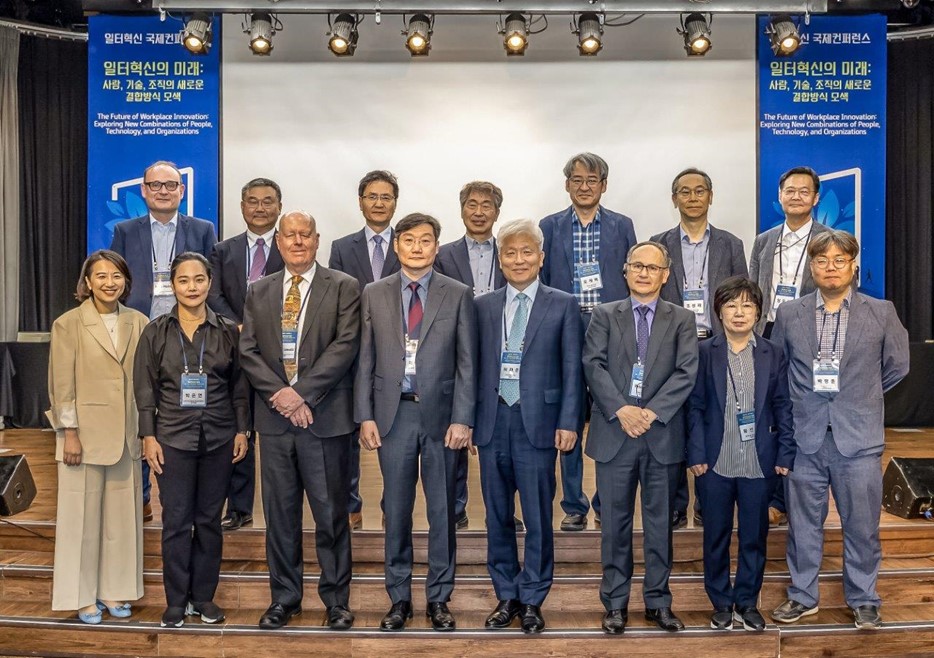
The WPI event further included a field trip to the southern industrial city of Changwon, where we visited two companies: LG Electronics and one of its suppliers, Ohsung.
LG presented its ‘Lighthouse Factory’, a newly built ‘smart factory’ producing a variety of types of refrigerator. Some 250 to 260 refrigerators are assembled per hour, with robots undertaking the major and heaviest tasks. LG has done an impressive job in applying digitisation, automation and reducing the ergonomic risks for employees. In terms of productivity, cost-saving, energy reduction and better services to customers the case is highly successful. And LG has succeeded in reducing the musculoskeletal risks for its workers. We were told that workers at other LG plants were applying for positions in this plant instead of their own. [See the YouTube footage of the LG Lighthouse factory below.
However, it was a somewhat disappointing case for WPI, especially from a western perspective. The Lighthouse Factory is a typical example of digital Taylorism: heavy tasks and unhealthy postures are automated but the remaining jobs on the line are characterised by a 13-second tact time interval per task. No formal education is required for the employees, and it is the speed of the production-assembly line that drives the work behaviour of humans.
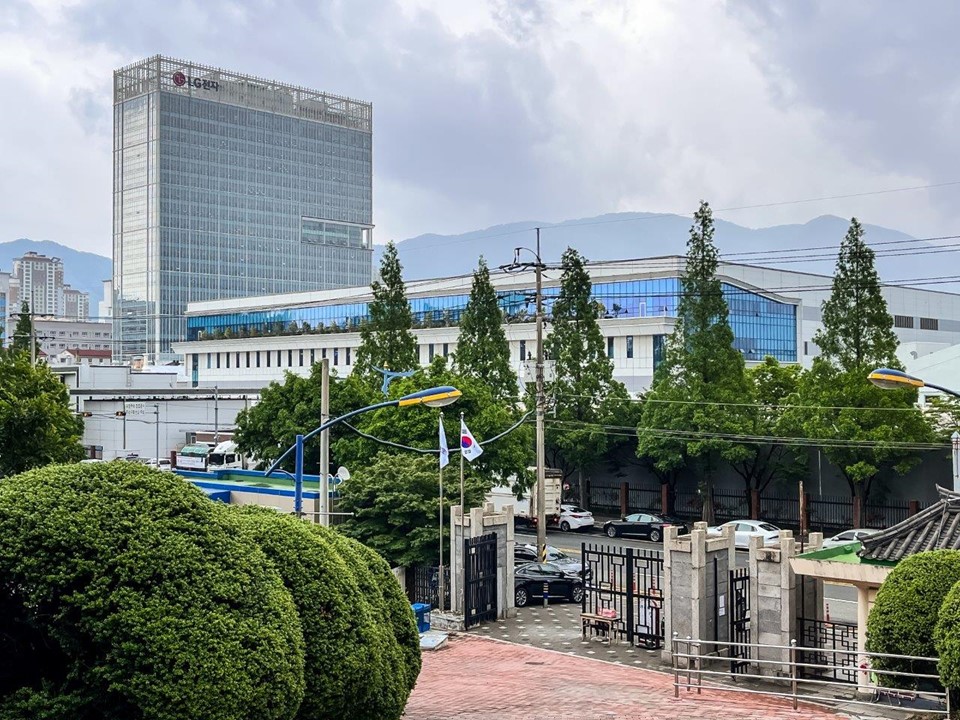
LG, Changwon
In short, nobody looked at the quality of work from the perspective of ‘active / complete jobs’ – jobs that offer learning possibilities and which enhance the employability and sustainable skilling of workers. ‘Full workplace innovation’ requires taking an integral, systemic look at what happens on the shopfloor.
The second company case was Ohsung, an LG supplier. Ohsung showed us an assembly line for washing machines parts made for LG. The company is dependent on LG for about 65% of its orders, and produces and assembles fully to specification. They assemble parts they manufacture themselves with parts they receive from LG. Again, we viewed a very efficient and digitalised assembly line, but the remaining human work, done mostly by a flexible layer of migrants from central Asia under contract to an external subcontractor, comprised low skill, repetitive tasks.
Interestingly then, whilst the hosts were convinced that they were showing us a work environment which embodied the ‘utmost respect for humans’, we need to convey a still stronger message by demonstrating what we really mean by ‘full workplace innovation’.
Despite the fact that both companies operate in highly competitive markets in which price (as well as from quality) competition is unavoidable, we feel there is a task for us to make clear the benefits of a longer-term view. Evidence and experience demonstrate that the innovative capability of firms also depends on the input of skilled and empowered staff. A ‘high-road’ perspective, in which win-win outcomes are sought for employees and the company alike, is difficult to achieve in such firms given that employees play only a limited role when it comes to participation in change and renewal. Whilst we were told that ‘quality circles’ and ‘continuous improvement’ stimulate employees to deliver ideas for improvement, participation in the redesign of the shopfloor is, in the case of LG at least, largely the domain of engineers and managers. Consequently, it comes as no surprise that the work organisation remains Tayloristic.
The debates continued during a workshop later in the week in which Peter Totterdill was asked to demonstrate the practical application of workplace innovation to around 50 consultants, drawing on his experiences of working with companies in the UK and elsewhere.
Across the world, there is a growing thirst for know-how in the creation of jobs that use and develop the full range of employee knowledge, skills and ingenuity at work. Whilst there are some differences in approach between Europe and Korea, it is clear that variations in national culture are no impediment to forging better ways of working, and to learning from each other.
The question thus remains how the EUWIN community can better support Korean businesses to implement ‘full workplace innovation’ instead of only improving the physical working environment for employees. Nonetheless, we are very grateful that our Korean hosts, who provided us with valuable insights in their companies.
Share This Story!
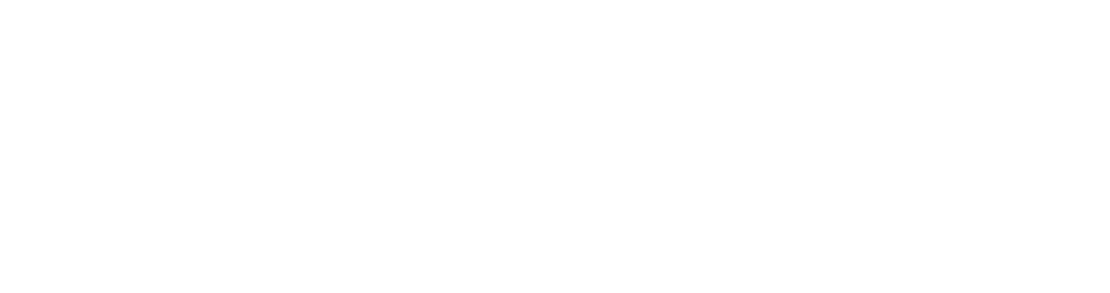
European Workplace Innovation Network (EUWIN)
EUWIN was established by the European Commission in 2013 and is now entirely supported by contributions from an international network of partners co-ordinated by HIVA (University of Leuven). EUWIN also functions as a network partner for the H2020 Beyond4.0 project.
Contact: Workplace Innovation Europe CLG (contact@workplaceinnovation.eu).