FSW Coatings Case Study
Context
This case study describes the union-management partnership at FSW Coatings, Ireland’s largest indigenous paint company founded as a family business in 1950. FSW underwent a sustained transition over a period of 9 years as the result of a collaboration between the company’s management team and SIPTU’s IDEAS Institute.
SIPTU, Ireland’s largest trade union, established the Institute for the Development of Employees Advancement Services (IDEAS) in February 2001. Its primary focus is workplace innovation, education and research (particularly research involving workers, employment and trade unions). IDEAS’ principal role is to identify ways in which new thinking and new services can be introduced into the workplace for the benefit of employees and the enterprise as a whole. IDEAS began its involvement with FSW Coatings in 2015, stimulating a remarkable self-sustaining momentum of change within the company.
FSW manufactures, develops, distributes and sells coatings and related products to professional, industrial, commercial and more than 400 retail customers in Ireland and internationally. Located in a rural setting in Virginia, Co. Cavan, FSW employs more than 160 people, many of whom have worked in the company for a large number of years. The company hosts Ireland’s largest paint laboratory with over 15% of its personnel actively involved in Research and Development. Several R&D projects have been focused on sustainability, including the introduction of environmentally-friendly ranges and reducing the use of plastics.
Reflecting the company’s commitment to continual innovation and improvement, 18 high-level projects are currently under development including the construction of a new storage facility, streamlining the ‘accounts payable and accounts receivable’ process, reviewing e-commerce, and ERP system upgrades.
Employee participation plays an important role in shaping each of these initiatives.
As a major employer in the area, FSW is strongly engaged with the local economy and community. In addition to sourcing from local suppliers wherever possible, FSW’s community outreach includes significant charitable donations (often inspired by employees), sponsoring students into further and higher education, and the “Community Colour” campaign. The latter has led in recent years to the donation of hundreds of thousands of litres of paint to local organisations such as sports clubs, scouts and those working with disadvantaged groups.
FSW’s journey from a traditionally managed company to one in which employee participation is embedded as a core value was largely made possible by the establishment of mutual trust between SIPTU and the senior team, engendering a shared commitment to exploring ‘win-win’ outcomes. Above all, this case study demonstrates how union-management co-operation can generate a self-sustaining momentum of workplace innovation that becomes firmly embedded within the culture and practice of an organisation.
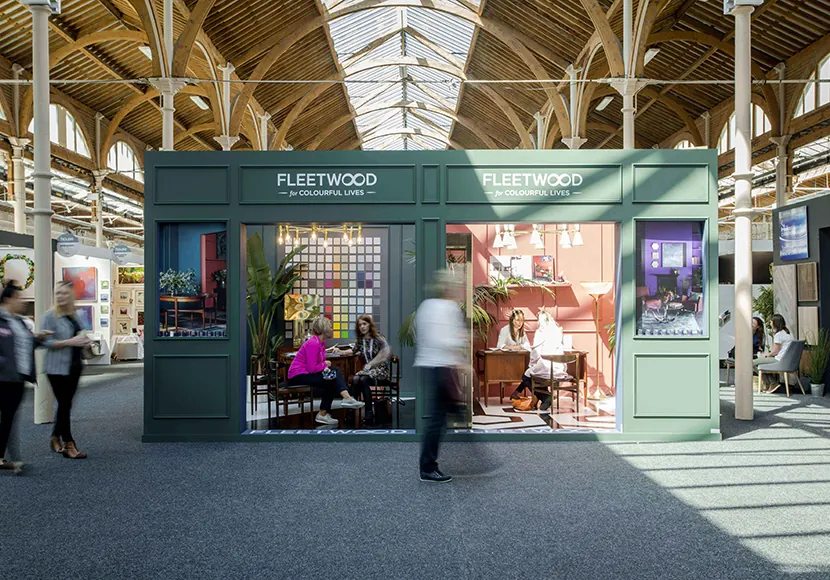
The Start of the Journey
In 2015 Tony Murphy, an experienced workplace innovation specialist in the IDEAS Institute, received a call from the Plant Manager to discuss the possibility of SIPTU assistance aimed at improving operational performance and quality in the face of growing competition from the multinationals. Tony travelled to Virginia to meet CEO Stan Buckley and other members of the management team, and to share the Institute’s experiences of working with other companies experiencing comparable challenges.
Despite some initial caution, Stan and his team agreed to invite Tony to deliver an initial training programme, bringing managers, staff and operators together to explore ways in which teamworking might be strengthened in the company. According to Tony, the course would enable them “to see what was involved and the potential benefits, and if they thought it was worthwhile, they would pursue it and we would work forward with them.”
The course focused on building effective teams in the workplace by equipping them with problem-solving tools and techniques. Course material was designed to be engaging and relevant, with a focus on learning from failures. For Tony, “the essence of the course is to develop teams that are good problem solvers.” He saw untapped potential in the knowledge and ideas of people across the workforce; for example, people in the mixing area know more than anyone about mixing, “we know the problems that we have every day, and we know the solutions too.”
“Natural” teams – people with different roles but working together in the same functional area – were encouraged to select and resolve specific sources of frustration they experienced in their day-to-day work. The course focused on root cause analysis, team dynamics and a collaborative approach to problem solving. It included tools such as brainstorming, fishbone diagrams and flow charting whilst at the same time placing emphasis on effective teamwork.
Examples of team projects undertaken within the course included the more effective management of paint returned to the factory because of damage to the tins, enhanced response times within the orders department, and improvements to the factory’s cleanliness and layout. These projects “won the heart of the company” according to Stan, “so everyone that was sitting down looking at a very simple 10 minute presentation understood, we’ve got a problem, we have a solution.”
The pilot training course was conducted over six full days, resulting in an accredited Level 5 qualification for each participant based on a formal assessment with a written exam, a learner’s journal, and a team presentation evaluated by the other teams.
Notably, course participants varied significantly in levels of previous academic attainment, yet the content was pitched at a level appropriate for all. For many, the award of a Level 5 certificate was a proud achievement.
Levels of engagement and the positive atmosphere that prevailed throughout the course were tangible, and its outcomes were well received by management and employees alike. Bringing senior managers and operators together broke down barrier and reduced the sense of hierarchy. According to Stan, “we were blessed, everyone loved what Tony was doing with us.”
As a result, further courses were then run for a 40+ additional people across the site, a programme designed to create an enduring legacy of effective, well-functioning teamwork in each production area.
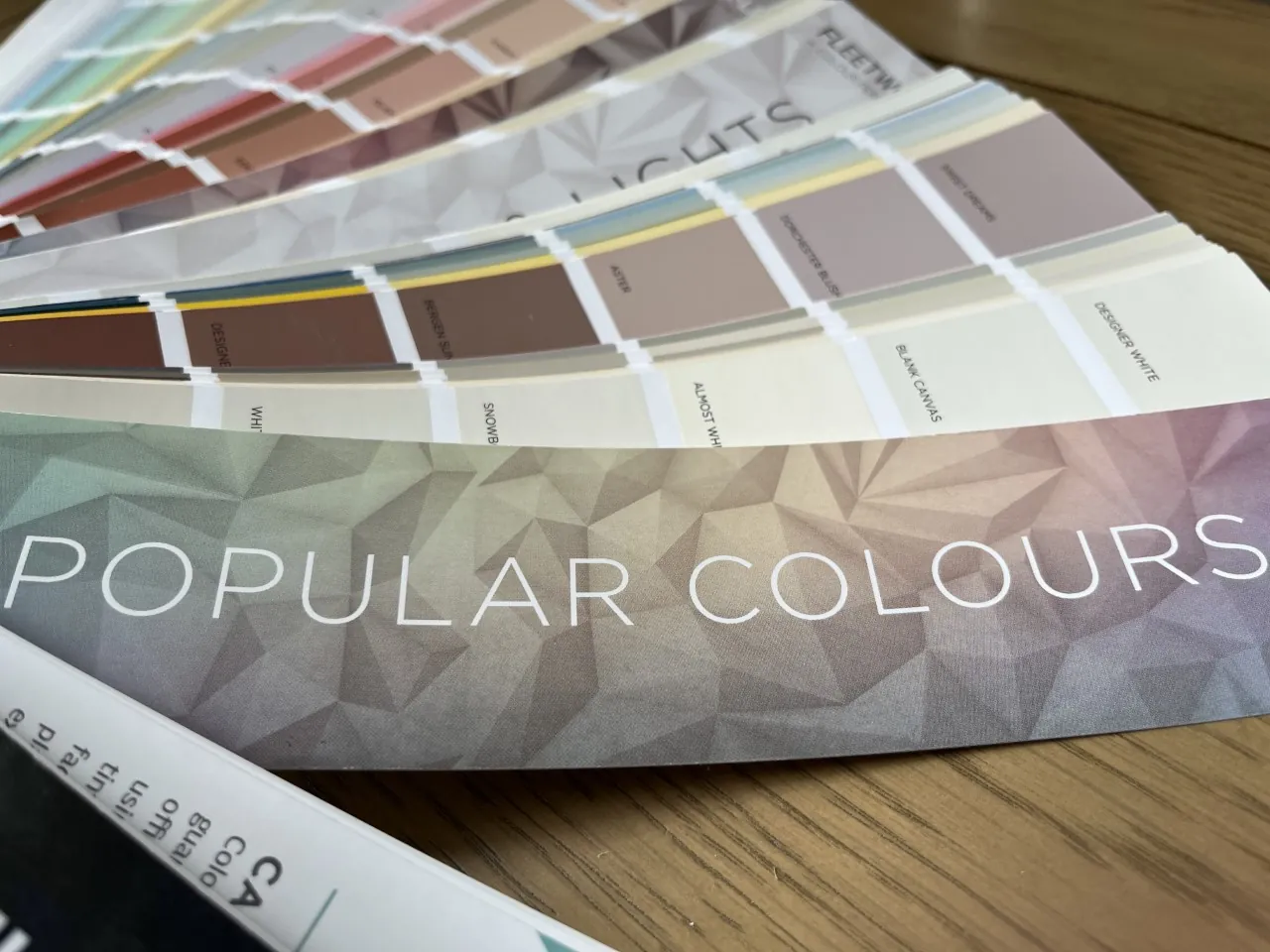
The Growth of Employee Participation
Much changed in the years following the courses, a journey that can be described as one of incremental transformation. Empowered by the insights and tools acquired during the course, operators and managers worked together to introduce several measures designed to enhance communication and teamworking.
Improving day-to-day communication featured strongly within the course, and several departments subsequently implemented regular ‘huddles’ – brief stand-up meetings during which teams share information and issues relating to current areas of work. Tuesday morning meetings which bring the CEO together with line managers include time during which employee suggestions are discussed. Periodic off-site meetings have also been instigated for key departments as an opportunity for wider reflection, review and improvement. One worker endorsed the changes, commenting that:
“There’s a lot more communication now between upper level management and anybody else, and the other way as well.”
Employee involvement in problem solving, improvement and innovation is an important part of the changes that followed Tony’s intervention. Stan is clear that the process established during the courses (“where we are we now, to where we want to go, and the process in the middle of it”) remains at the core of each project. “Any of the projects that the project team are looking at would be based on those presentations, but a little bit more elaborate as we’ve learned more models.”
Other improvement measures such as the accounts initiative referred to above are typically as inclusive as possible, involving frontline staff sitting down with managers to use the collaborative problems solving tools acquired during the course. According to one worker in the Colour Lab:
“There’s a lot of ideas out there that never see the light of the day. What we formed was a giant steering committee, where people could basically do a bit of a brainstorming, come up with ideas of how to improve various areas. So if this person knows a way to do something better, then he could do that particular task better.”
As Stan points out:
“It’s the staff that know how to run the plant, know how things actually happen. We can provide additional backup and resources, but really they know what the problem is.”
Beyond problem solving, employee-led innovation has led to significant developments at FSW, and does not rely on a traditional suggestion box. For example, Karina Hyland (the manager of the R&D department) came from a farming background, and knew that farmers needed to distinguish between those cows that were pregnant and those that were not. Farmers were buying significant amounts of specialised paint from New Zealand, used to mark the tails of those animals in heat and which rubs off during mating, enabling pregnant cows to be easily identified. She saw an immediate opportunity for import substitution. Karina recalls:
“I brought the idea to FSW and they were very much on board to see where the project went and to support it fully financially. And so they gave me the scope to get in discussion with a designer to come up with the design.”
Karina was given the time and resources to develop the paint plus a specialised applicator with her team. RainBó roller tail paint is now an important addition to the Fleetwood range.
Although such notable successes account for only a small percentage of ideas generated by employees, openness to new thinking is recognised by management as an important contributor to workforce engagement. Stan mentions that:
“One of our staff members wanted us to investigate putting solar panels because you’ve massive roofs here to start. That project will have him directly involved in it with two other two or three other people in the business, because he’s passionate about it.”
Another employee-instigated and led initiative is the creation by a team of employees of an attractive garden area outside the factory, “planted by people, employees in the business on their spare time, not getting paid.” The company also contributes to an Employee Assistance Plan, providing counselling and financial support to workers and their families in times of need, and run by volunteers from the workforce rather than managers to ensure confidentiality.
A further legacy of Tony’s courses is the establishment of a learning culture within the company, characterised by an openness to meeting individuals’ interests in acquiring new competencies and a constant flow of training from Masters’ level qualifications to lean ‘Green Belt’ training to the basics of Excel spreadsheets.
Notably, FSW’s organisation chart is relatively flat for a company of its size, reflecting a culture of trust and the avoidance of micromanagement. John Hetherton, Fleetwood’s Technical Manager, says,
“You know, we all have our jobs to do, but if you try to micromanage people, then it just becomes a mess. And if you can say to person A or B, this is what I want and this is what good looks like, I’m not going to go down and look over your shoulder every day.”
Stan points to the ripple effect of the changes since 2015. Around half of FSW’s workforce are external to the plant – in shops and trade centres as well as peripatetic sales staff and technical specialists,
“Now none of those people have participated in the training, but the fruits of that have all been shared around the place. And you can see it, without a doubt.”
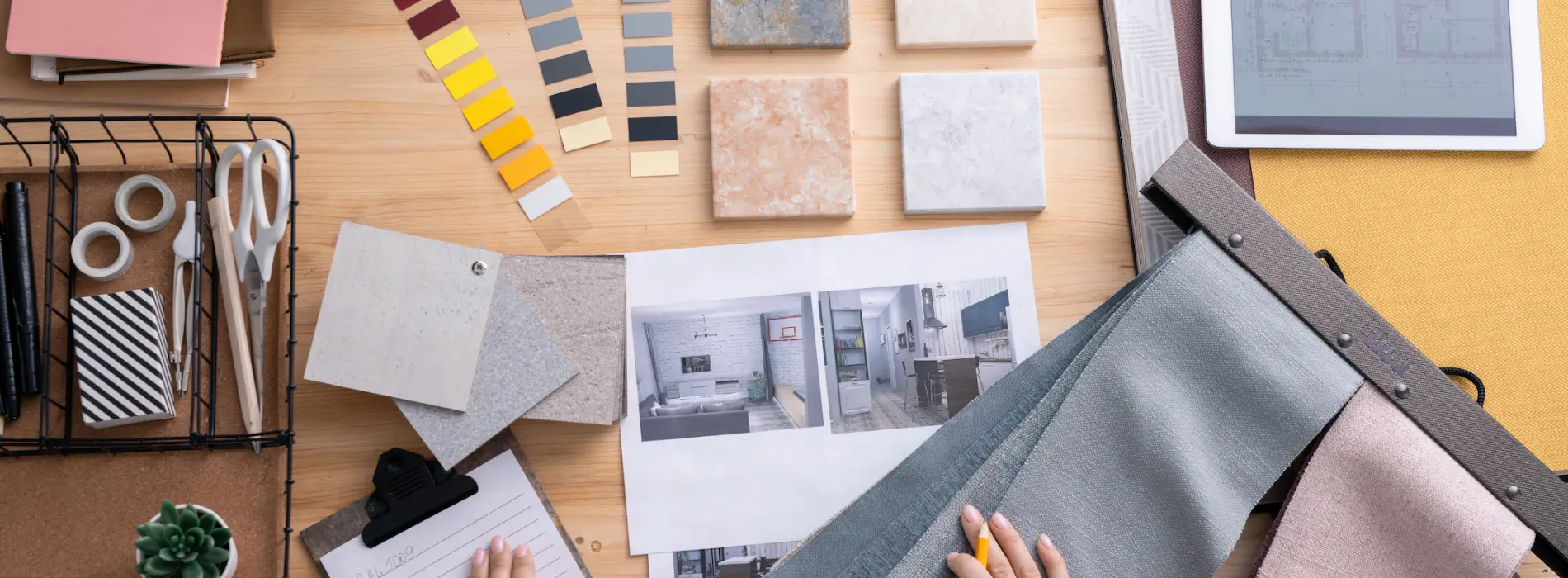
Introducing New Technologies
The introduction of two new robots to the production floor provides a key example of employee participation in technological innovation. The introduction of a state-of-the-art palletizer (used for the automatic stacking of cases of goods or products onto a pallet) involved extensive participation by members of the filling team, enabling the removal of some arduous physical tasks and leading to significant improvements in employee productivity.
Four staff, including operators, were sent to Spain to provide input to the robot manufacturers, ensuring that the design was ergonomically suitable for them, and making them feel both valued and part of the process. This also helped the team understand the new technology as well as its benefits.
Operators were upskilled to programme and use the new robot. Four developers and programmers visited the factory from Spain to collaborate directly with operators in the deployment and initial operation of the machine. Kieran O’Carroll (Production, Environment, Health and Safety Manager) points out that in terms of day-to-day operation:
“The guys on the floor very much have the decision on that rather than the company. And we kind of work around that. They get very much involved in it and it feels like it’s their machinery rather than the company’s.”
For FSW, this level of operator autonomy and control significantly reduces the need for management intervention whenever something changes, for example the introduction of a different size of paint can.
Kieran is clear that there is more potential for automation: “And so where we can improve efficiency and improve welfare, that’s very important to us”, but not at the expense of jobs. Human skills and intuition remain vitally important. John says that paint-making remains something of a “black art” despite all the technological advances:
“You can look at a formulation but without understanding the nuances of that, it’s difficult then to be able to get it to achieve the results that you want. That comes from working with the product for so many years and trying to understand that if I make an adjustment here, that’s obviously going to affect something else.”
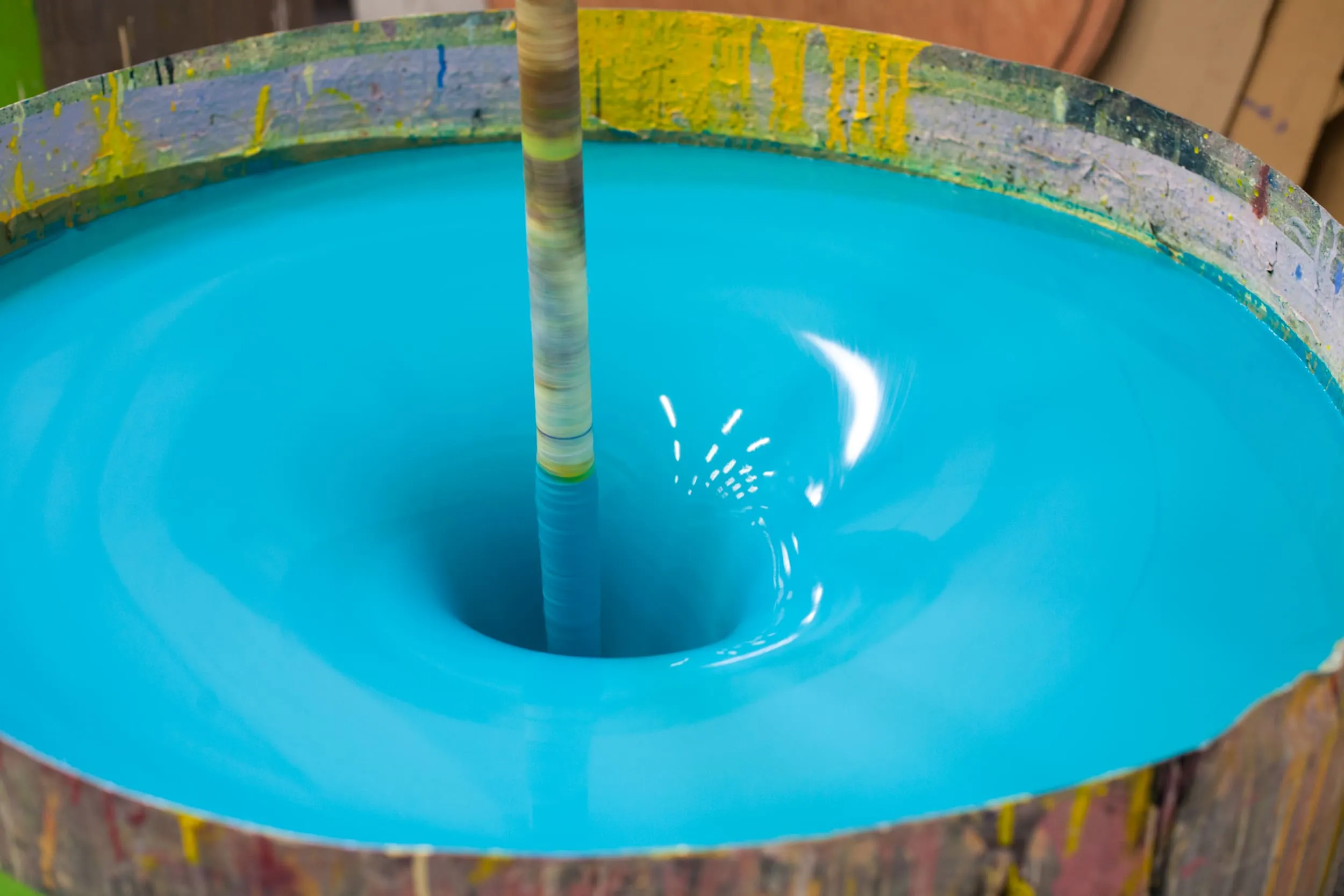
Learning the Culture
Stan is optimistic that the established culture will survive as long as the business remains family-run. The founders built the business on relationships, and the current owners try to treat everybody as if they were their own family member. Stan and Tony both describe this in terms of “Irishness”: awareness of other people’s feelings and looking after each other, a national cultural characteristic which the company tries to maintain in business practices and interactions with employees.
Stan explains that new employees receive a basic induction into the business operations, but that the culture is something they experience and learn through interactions with colleagues and management.
The culture of the business also influences FSW’s recruitment process, which is based on attitude and values as much as skills. They sometimes pass over highly qualified candidates if they do not fit the family business culture, and look for team players who are respectful to colleagues at all levels.
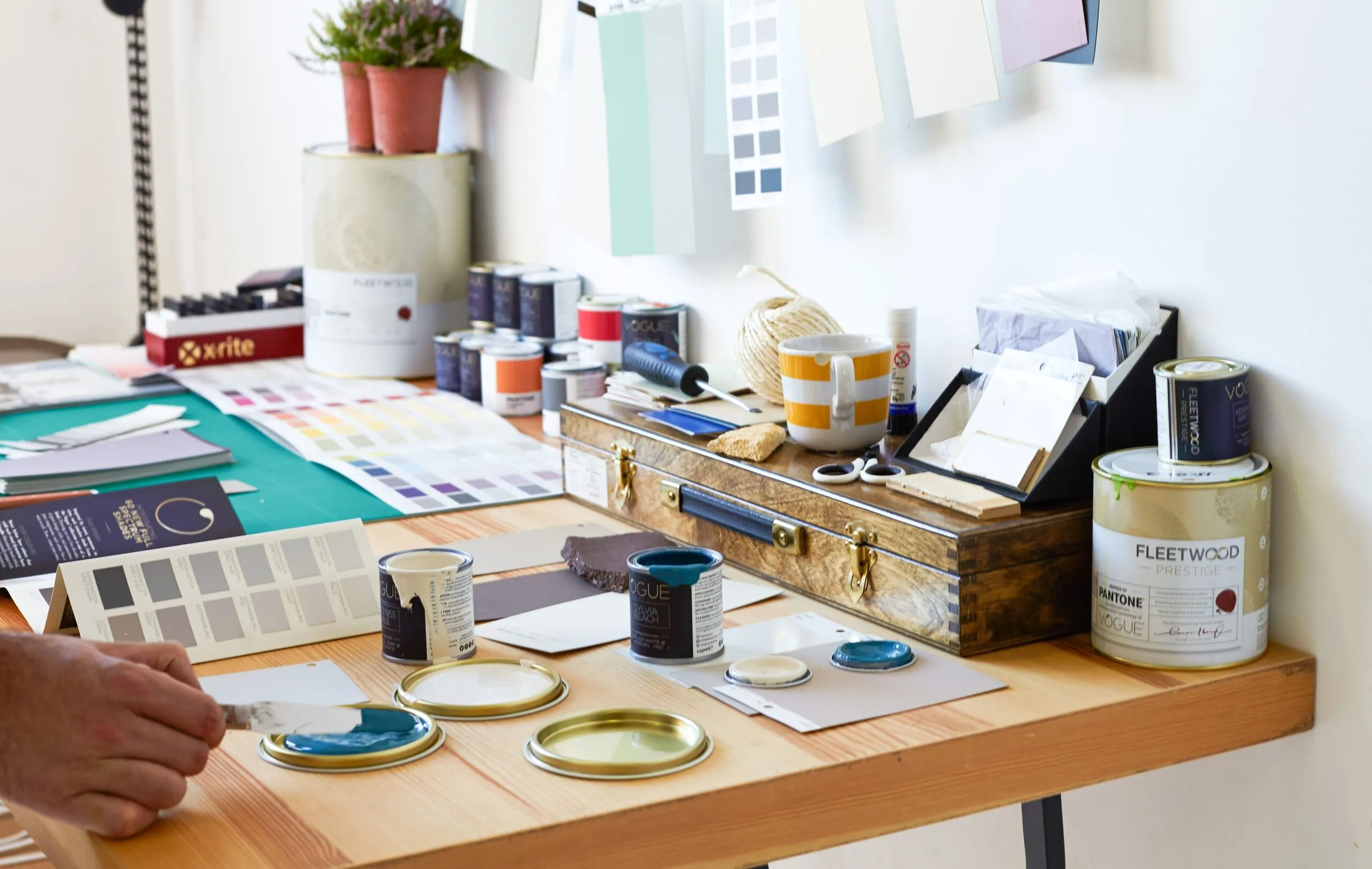
Learning from the Transition
FSW offers compelling evidence that a time-limited but highly structured period of collaboration can lead to a sustainable momentum of change, with employee participation at its heart. Significantly Tony’s practical support for FSW ended in 2016 and did not return to the company until the BroadVoice research visit in 2024, yet the internal drive for change was sustained throughout the intervening years.
Such evidence is not however commonplace, so it is important to understand the underpinning success factors at FSW. Not only was Tony an experienced change facilitator in his own right, but he also represented the trade union recognised by the company. This helped to overcome the major barriers of employee trust and engagement typically found at the inception of such change processes.
Ireland’s social partnership was severely diminished by 2015 but this did not affect the trust and co-operation between SIPTU and management at FSW. Doubtless this facilitated acceptance of Tony’s initial proposal and eased his pathway into the company.
Nonetheless, for employees and management alike, the achievement of relatively “quick wins” as a result of the initial course played an important role in creating enthusiasm and subsequent commitment to the programme.
Stan emphasises the impact of leadership behaviours on organisational culture, and especially the importance of self-awareness: “If you’re self-aware, then you can go and tackle any other issues that you want to. You don’t start by changing culture. You look at yourself first, and you change the things that change the culture.”
One frontline worker commented:
“Something’s working because there’s more demand for our products now, even though the economy is basically the same as it has been five years ago. It’s just made people more aware that, look, you can do things better here and constantly strive to improve instead of just going along and producing a product week in week out and just sticking to that. So you have to keep changing and moving forward. Otherwise you’re going to be overtaken by the competition.”
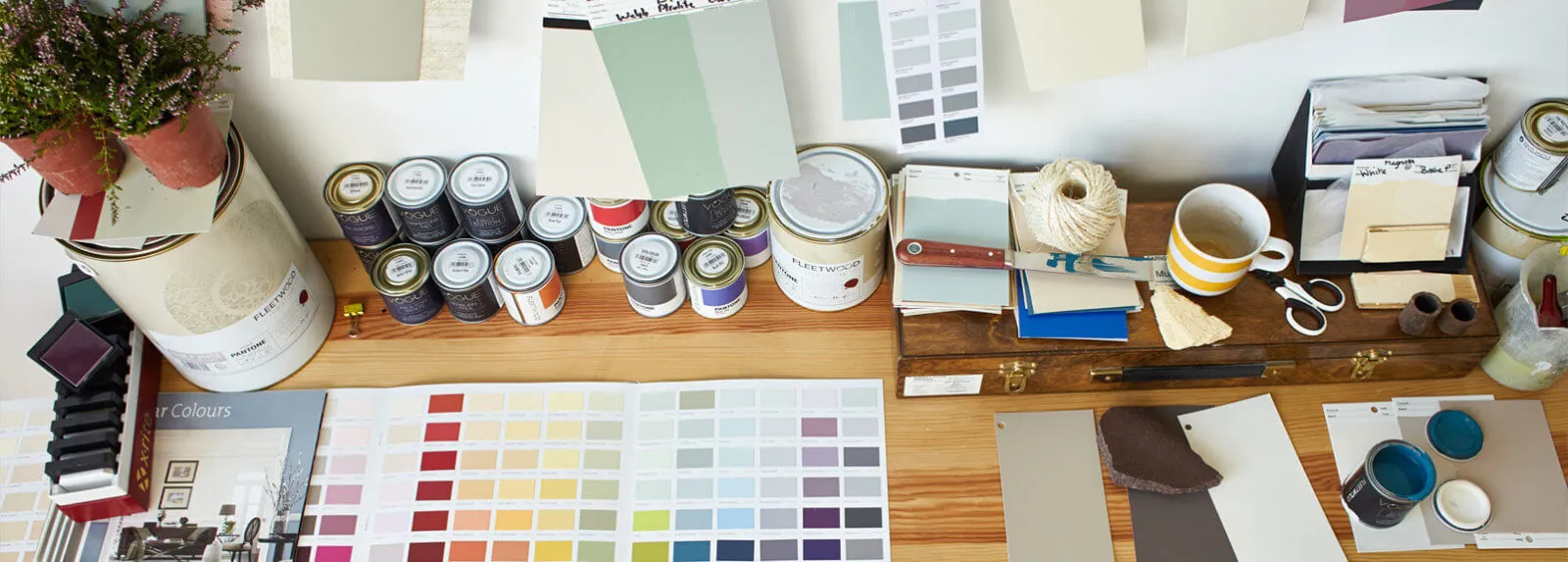
Share This Story!
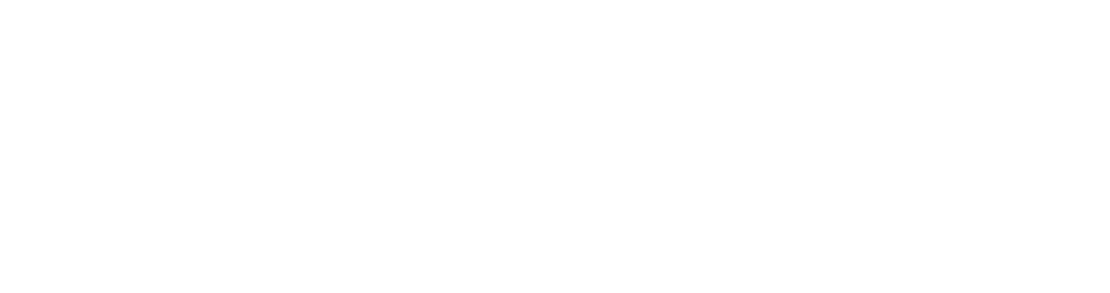
European Workplace Innovation Network (EUWIN)
EUWIN was established by the European Commission in 2013 and is now entirely supported by contributions from an international network of partners co-ordinated by HIVA (University of Leuven). EUWIN also functions as a network partner to BEYOND4.0 and BRIDGES5.0 projects.
Contact: Workplace Innovation Europe CLG (contact@workplaceinnovation.eu).